Big Plans for Large-Format Printing
Massivit is launching new large-format 3D printers for parts and tooling.

The Massivit 10000 is targeted at compositing tooling applications. Image courtesy of Massivit.
May 11, 2021
At the AMUG conference in Orlando last week (one of the very first conferences in the industry to make a return to in-person attendance here in the U.S.), Massivit 3D Printing Technologies unveiled its new industrial grade Massivit 5000 printer. The new unit can produce parts up to 57x44x70-in., and can accelerate the production of parts, prototypes and tooling by up to 30 times compared to other technologies, according to the company.
Coming at the end of 2021, the company has another major product launch—the Massivit 10000. That device is another large-format printer targeted at reducing the mold production time for large tooling in the composites manufacturing space.
We spoke to Ido Eylon, vice president of global sales at Massivit 3D, to find out more about both devices and the proprietary technology that has enabled their development.
You announced the Massivit 5000 before the conference, but AMUG was the first chance a lot of people had to see it. How did that go?
Ido Eylon: It was amazing, because this is a new category of manufacturing technology that is very unique to us, invented by our founder, and there is no other company that uses this technology to make 3D printed parts. We have an advantage in speed and size. This is a category that people are not really already familiar with.
How does that technology—the Gel Dispensing Printing technology—lend itself to large format printing?
The material is at the heart of the innovation. The gel material is UV curable. UV-curable materials are well known, but usually as a liquid. This one starts off as gel, and the mechanical properties in its raw state allow us to print much faster. Thanks to the fact that it is curable, we can also cure it and set it instantly, so that basically allows us to put layers on top of each other much faster and cure them, and also to print in self-supporting angles that were not possible before. We can print hollow geometries, which is faster and more cost effective.
What can you tell us about the Massivit 10000?
With our GDP technology, we already have that on the market and have more than 140 units out in the world based on GDP.
The Massivit 10000 is based on that concept. Since we can print a hollow structure, we can print two walls. There is a third printhead, which is not gel dispensing, but a Cast-in-Motion (CIM) head that will put casting material between the two walls that we print. We can print a sacrificial shell with gel material, and every few layers or so, the Cast-in-Motion head will fill material in between them.
We are very much focused on creating tools for composite materials molding. We can significantly shorten the cycle time and also cut costs for the production of molds for composite materials. The casting material that we currently use is epoxy based, and it is the right material for this application. Later on there will be more materials enabled on this new technology, and that will be for futuristic applications.
How have you managed to continue to bring these products to market, given the supply chain disruptions and travel restrictions during the pandemic?
It was very hard to interact with people the way we used to. We just finished this very successful conference at AMUG, but to get that kind of exposure last year was impossible. We did Zoom and online demos, but that did not get us nearly a fraction of the exposure we got at AMUG.
Another challenge was the impact the pandemic had on our customer base.
We went public earlier this year and raised funds on the Tel Aviv Stock Exchange. We believe that will help us execute our long-term strategic plan to bring products to market, and to continue to develop new products and transform the way big parts are being made.
Subscribe to our FREE magazine,
FREE email newsletters or both!About the Author

Brian Albright is the editorial director of Digital Engineering. Contact him at de-editors@digitaleng.news.
Follow DE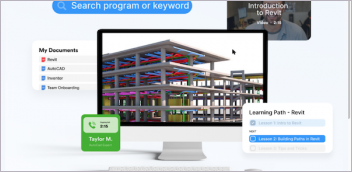
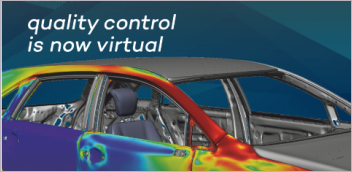
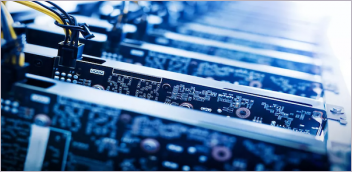
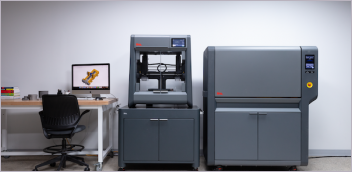