Virtual Reality Speeds Design

Engineers can place the virtual model in a variety of realistic environments, including roads, urban landscapes and vehicle showrooms. Image courtesy of Ford.
Latest News
August 3, 2015
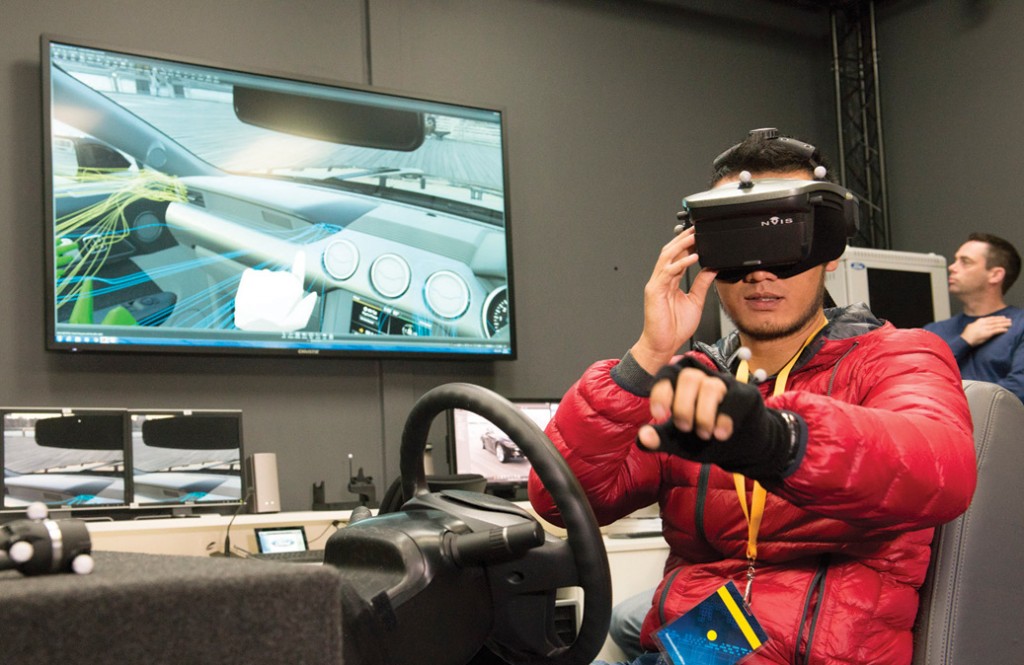
Ford Motor Company is leveraging virtual reality technology to eliminate many of the design challenges faced by today’s automobile manufacturers. The company, which says it is the first automaker to use ultra high-definition immersive virtual reality, has made impressive strides in speeding up the design process and prototyping products without having to physically construct them first.
The secret behind the company’s success comes in the form of the Ford Immersive Vehicle Environment (FIVE) Labs. The FIVE Labs function as virtual vehicle prototyping rooms. They include a dummy car rig with a seat and steering wheel, an 80-in. 4K monitor and a computer rig.
Users wear a pair of VR (virtual reality) goggles and a glove, each of which are monitored by 19 motion tracking cameras dotted around the walls to capture the precise location and orientation of the wearer. The goggles allow users to observe realistically interpreted CAD models of a vehicle, which can be placed in a variety of different environments. The users can walk around the virtual vehicle, as if it was parked in an actual environment, such as a new vehicle showroom.
“We now have Ford designers and engineers around the world working together virtually—inside and side-by-side—on the same product,” says Elizabeth Baron, Ford Virtual Reality and Advanced Visualization technical specialist. “By using this technology, designers and engineers can quickly transition from one car design proposal to another, and they can study and identify which is the best option.”
Users can also sit down in the test rig and experience the interior of the vehicle. Baron describes this experience as “uncanny, and feeling just like sitting in a real car.” She says the level of detail is extraordinary. Ford uses the virtual rigs to test for quality, engineering issues, fit and finish of the CAD designs long before engineers move toward creating a clay model or any other physical prototype.
A New Approach to Design
Baron describes the virtual lab as a collection of high-performance computing (HPC) components, which are integrated with advanced simulation software elements to create a 3D virtual world that allows designers and engineers to experience automotive designs. Simply put, by using a totally immersive virtual environment, Ford’s designers and engineers can experience a vehicle the same way a customer would in a showroom.
Beyond the immediate benefit of visualizing design changes before actual production, the virtual lab offers many other advantages. For example, engineers collaborate in real-time, simultaneously experiencing the same point-of-view. By creating a shared 3D virtual reality, Ford’s designers and engineers are able to quickly overcome traditional design challenges. The lab also allows multiple designers and engineers from different geographic locations to work together in real-time on vehicle design, without having to travel to a central location. Ford has accomplished that by integrating the virtual immersion capability of the virtual lab across multiple locations.
“Thanks to a host of recent upgrades to the lab and its establishment in other Ford development centers around the world, Ford became the first automaker to use the technology on a global level, thereby enabling simultaneous input from designers and engineers working on the same product at the same time,” says Baron.
Throughout 2013, Ford designers and engineers examined over 135,000 details on 193 virtual vehicle prototypes, all of which were virtually built in the Immersion Lab. “Such an achievement would have been impossible just a few years ago,” says Baron.
The benefits of 3D immersive design validation have become easy to identify and have been demonstrated by delivering improvements for the customer in such vehicles as the Ford Fusion and 2015 Ford Mustang. For example, engineers were able to examine the placement of the side view mirror and rear brake light in the Ford Fusion before creating a physical representation of the vehicle.
In the case of the side view mirror, the goal was to optimize visibility without impacting the design of the car. The position of the side view mirror went through several virtual iterations before the team decided that a door-mounted design was optimal. The LED center brake light underwent a similar process, with engineers determining that an ultra-thin unit maximized visibility without losing style.
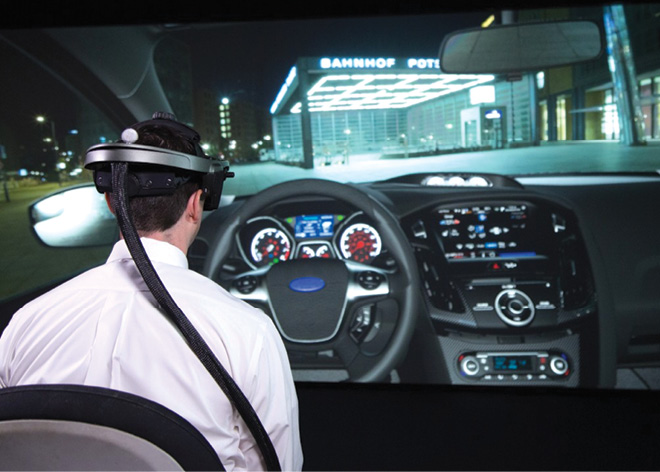
Baron and her team were able to offer several other solutions to design problems before any production or physical prototyping took place. Those improvements ranged from the placement of pedals in right-hand drive vehicles to the integration of entertainment systems and environmental controls.
The benefits derived from the system have led Ford to expand the capabilities of the FIVE labs since their introduction as a proof of concept. The transition from concept to reality actually took place very quickly, even though Baron faced several internal challenges.
“One of the most difficult goals was getting buy in from various departments. We had to convince stakeholders of the viability of the technology and overcome the resistance to adopting virtual design concepts,” says Baron. “However, users have quickly realized the benefits offered and have had a profound realization that observing a vehicle’s design using a 1:1 relationship is far superior to looking at numbers on an Excel spreadsheet.”
Constantly Improving Technology
Ford continues to improve and distribute FIVE Lab technology by adding it to design centers in Australia, Germany, China, India, Brazil and Mexico. Recent enhancements to the system include 4K “power-wall” displays, which offer four times the resolution of a high-definition television, enabling Ford designers and engineers to better evaluate and review 3D models of vehicles in real time, globally.
“We moved to the global One Ford plan so that international collaboration could lead to the development of globally appealing vehicles,” Baron says. “With this technology, designers and engineers can enhance their ability to achieve that goal—while also improving vehicle quality.”
New software enables engineers to study hundreds of elements inside and outside of a vehicle, ensuring that vehicles coming to market “have been painstakingly inspected for usability, consistency and design effects that are now discernible in the sophisticated shadows and real-world lighting conditions the tools provide,” according to Ford.
“Other enhancements, such as the new 4K-resolution power-wall, give Ford engineers a life-sized view of issues that arise in vehicle development. That life-sized view is further enhanced by pairing the actual movement of designers and engineers with virtual movement, regardless of their physical location,” says Baron. “The system links Ford workers globally to simultaneously analyze and inspect the same virtual vehicle on a scale not possible before. The newest software provides a virtual experience almost indistinguishable from a real vehicle.”
In its quest to improve the immersive experience, Ford has deployed a technology called the Programmable Vehicle Model, which allows engineers to be immersed in a lifelike virtual vehicle. Content evaluators are able to sit in the Programmable Vehicle Model, which consists of an interior laid out with a steering wheel and seats, and be able to both visualize and feel components.
Engineers can test steering wheels, door handles and other major touch points for placement relative to the driver’s seat. The Programmable Vehicle Model supports many virtual 3D capabilities, allowing designers who are located outside of the vehicle in the Virtual Space to collaborate with others, who may be inside the Programmable Vehicle Model.
Furthermore, the Programmable Vehicle Model is integrated with a cave automated virtual environment (CAVE), which provides a wide field-of-view virtual environment, allowing Ford engineers to rapidly test design and placement components to study visibility and customer preference.
Beyond the FIVE Lab
Even though the equipment used in Ford’s labs is highly specialized, the applications for virtual reality-based product design are vast. Rave Computer, which provides some of technology for Ford’s FIVE Lab, is helping companies and government organizations create in a more immersive environment with its RAVE CAVE—also known as the Reconfigurable Center for Automated Virtual Environments.
Located in Sterling, MI, the RAVE CAVE is run as a non-profit organization through a research partnership between Rave, TARDEC and DC3S. Through this collaboration, the agencies promote modeling, simulation and visualization technology, creative R&D and STEM education. In addition to giving small- and mid-sized firms access to virtual prototyping capabilities, the CAVE also provides software companies the chance to develop and perfect their own platforms. Current software providers include Autodesk, Intel, ESI Group, RTT (now Dassault Systemes’ 3DEXCITE) and Mechadyne.
By using the CAVE for product design and testing, users have access to scenarios that might not be possible with a physical prototype. For example, engineers can place an automobile in many different environments. Within the CAVE, they can see how the car reacts to different weather conditions, a process that would traditionally require extensive physical testing over a long period of time. However, the CAVE enables teams to view all of these scenarios within several hours. “It lets engineers get a lot further along without creating a physical prototype than they otherwise would be able to,” says Matt Moy from product development at Rave Computer.
Additionally, since the technology at the CAVE is all encompassing, users can see designs in a whole new light. The company recently showcased a model of the human body to a group of physicians. “These physicians were not only able to see the body, but place their head [in it] and view the heart from the inside out,” says Rick Darter, president and CEO at Rave Computer. “[The technology] gives you that immersive capability of seeing underneath, inside of, as well as the actual figure of what you’re trying to demonstrate.”
Looking Ahead
Moving forward, this type of technology is expected to become more mainstream as firms find more uses for immersive visualization environments. “If you’re an engineer and you’re designing something, it’s pretty much a no-brainer to take the opportunity to look at [the product] before building something to look at. And so as the cost of the technology comes down, the use of this technology is increasing,” says Karl Rosenberger, director of product development at Rave Computer.
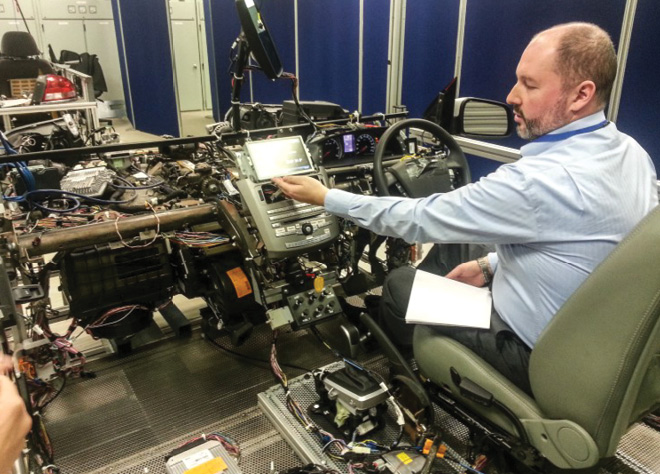
As Ford comes to rely on virtual immersion as part of the design process, many of the engineers are requesting additions to the experience, creating a rapidly evolving virtual working environment.
“One of those additions came in the form of adding ‘X-ray vision,’ which gives users of the immersion lab the ability to see inside and through a vehicle structure to study how various structural, mechanical and electrical systems interact within the architecture. Our new technology is more refined, and allows us to see and understand complex engineering issues while considering aesthetics and design,” Baron says. “We are incorporating light and shadow calculations in real time, which adds more depth and authenticity.”
Baron is quickly able to highlight the benefits of the system, including what she calls “a holistic approach to vehicle design” and “a profound realization of vehicle design.” As the system stands now, new vehicle designs can be imported and visualized in a matter of days, accomplishing what once took many weeks to create clay models and mockups of features.
Those benefits have led Ford to further expand its technological design capabilities, including the recently created Ford Research and Development Center in Silicon Valley. The new center is helmed by Dragos Maciuca, a former Apple engineer with experience in consumer electronics, semiconductors, aerospace and automotive technology.
Ford plans to build a team of 125 professionals under Maciuca, which would make the company one of the largest dedicated automotive research teams in the valley.
“We want to create a collaborative environment, an environment that’s very unique to Silicon Valley,” says Raj Nair, vice president of global product, Ford. Indeed, some of the projects that are already underway include collaborations with several universities and technology companies.
More Info
Subscribe to our FREE magazine,
FREE email newsletters or both!Latest News
About the Author
Frank OhlhorstFrank Ohlhorst is chief analyst and freelance writer at Ohlhorst.net. Send e-mail about this article to DE-Editors@deskeng.com.
Follow DE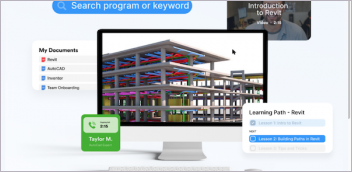
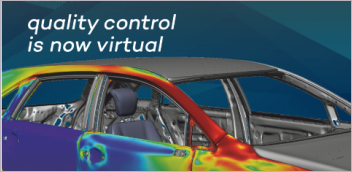
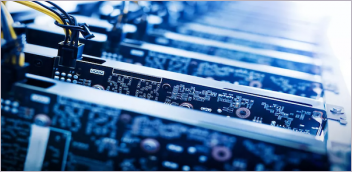
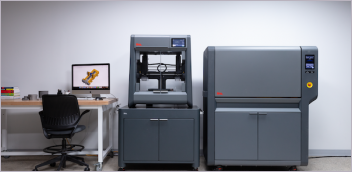