
March 31, 2022
Since its creation in the 1980s, 3D printing has evolved tremendously, with more printing technologies and material types available. Research shows that engineers in North America are optimistic about the future of 3D printing and believe new materials will help advance the industry.
Injection molding is the most widely used processing technology for plastics (Guevara-Morales & Figueroa-López, 2014); however, it does have its limitations. For example, parts with hollow walls or other complex geometries cannot be produced (Styles, 2018), and small production runs can be very expensive. Luckily, additive manufacturing – also known as 3D printing – can be used as an alternative manufacturing method.
3D printing was once perceived as a process that was only suitable for rapid prototyping, but that is no longer true. In 2019, a French 3D printing company called sculpteo surveyed more than 1,300 people from around the world – 64% of which had an engineering background – to determine the current state of the 3D printing industry. The study found that 51% of respondents use 3D printing for production, up from 38% in 2018. Additionally, nearly 60% of respondents believe the industry needs new materials to grow. This white paper examines a new engineered composite plastic material solution for the 3D printing industry: powders and filaments capable of producing plastic parts that are nearly as durable as certain injection-molded components.
Fill out the information below to download the resource.
Latest News
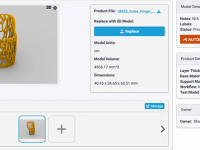
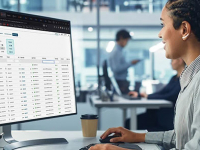
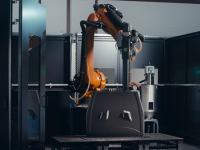
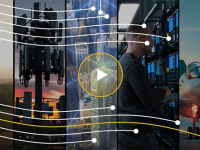
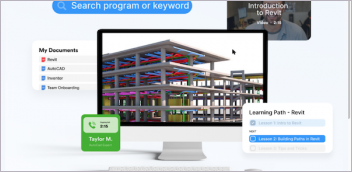
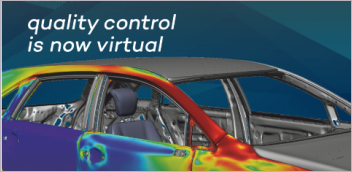
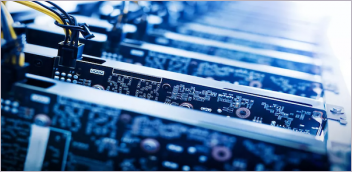
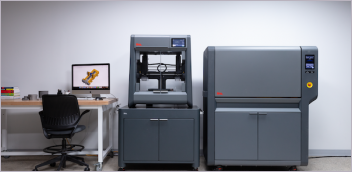