3D Printing Wear-Resistant Components With ESD Properties
With iglide® I8-ESD, igus is launching an SLS material that enables the additive manufacturing of prototypes, series parts and spare parts with ESD properties.

Latest News
April 13, 2022
Every machine contains moving parts that cause friction. In contrast to metal, components made of wear-resistant iglide® plastics do not have to be lubricated since solid lubricants are embedded into the materials. However, polymers cannot dissipate the electrostatic discharge (ESD) caused by friction.
In semiconductor and electrical engineering, a static discharge through components can lead to permanent damage to the product, even if the discharge cannot be felt by humans. In order to protect these components permanently from irreversible damage, a controlled discharge is necessary. Materials with defined surface resistances that are neither insulating nor conductive, i.e. antistatic or static dissipative, must be used.
What are the characteristics of an ESD material?
The friction between two insulating materials causes ESD. We encounter this physical phenomenon in everyday life - for example, when lightning strikes during a thunderstorm, when we touch door handles or when walking over carpets with plastic shoes.
The surface resistance for the ESD area must therefore be less than 1012 and greater than 106 Ohm; otherwise, the material is considered to be insulating or conductive. In most of the material data sheets, the electrical properties are specified by the characteristic values spec, volume resistance (Ωxcm) and/or specified as surface resistance (Ω). [Source: Technical article: ESD - the invisible danger , ELV Journal 04/2010, Matthias Schmidt ]
The material properties of iglide® I8-ESD
The new laser sintering material iglide® I8-ESD was specially developed for applications in which the dissipative electrical material properties are to protect sensitive electronic components.
In addition to the static conductivity, iglide® I8-ESD has a high abrasion resistance compared to a standard PA12 laser-sintered material, making it ideal for all applications in which electrostatic charges have to be avoided. Here are the outstanding properties at a glance:
- External lubricant and maintenance-free
- High abrasion resistance
- Electrostatic dissipative (ESD)
- Color: black (throughout)
- Increased rigidity
- Available as SLS powder or a 3D-printed component in 1-3 business days
The material data sheet for iglide® I8-ESD is available for download here.
Wear properties in comparison
Like all iglide® materials, iglide® I8-ESD has also been tested numerous times to optimize its coefficient of friction. The high abrasion resistance of iglide® I8-ESD was confirmed in practical wear tests. Whether in linear or pivoting application, iglide® I8-ESD shows, for example, a factor 2 better wear rate than regular SLS materials in pivoting.
Below are test results from the igus® laboratory, iglide® I8-ESD in the swivel wear test. (Translation: Wear Swivel 2 MPa 0.01 m/s & Wear Rate μm/km. iglidur® is another product name for iglide
Below are test results from the igus® laboratory, iglide® I8-ESD in the linear wear test. (Translation: Wear Linear 1 MPa 0.01 m/s Stroke Path 5mm & Wear Rate μm/km. iglidur® is another product name for iglide®)
Why is the conductivity slightly directional?
The mechanical parameters in most materials for the powder bed-based laser sintering process are direction-dependent (i.e. anisotropic). The tensile strength in the XY plane is often many times better than the XZ / YZ plane produced in the construction direction. In practice, the layer strength in the plane is thus higher than the strength between the layers.
The electrical conductivity of plastics depends not only on the concentration of conductive fillers but also on the particle distribution in the plastic. The process-specific layer application during laser sintering using a doctor blade or a roller leads to an increased alignment of the fillers and, overall, to a greater inhomogeneity of the filler distribution.
The measured electrical conductivity in the direction of construction is therefore lower (higher surface resistance). For iglide® I8-ESD, the direction-dependent difference in the specific volume resistance is between 3.4x106 Ωxcm and 2.8x107 Ωxcm (See data sheet). However, the differences are within the range for ESD-compatible materials.
Buy iglide® I8-ESD as a material or have components printed
Since iglide® I8-ESD is suitable for processing on regular laser sintering systems, it can be purchased as SLS powder and processed in your own printer. If you do not have your own SLS system or only need a few parts from it, you can order the components from the igus® 3D printing service. Delivery takes 1-3 business days.
More Igus Coverage
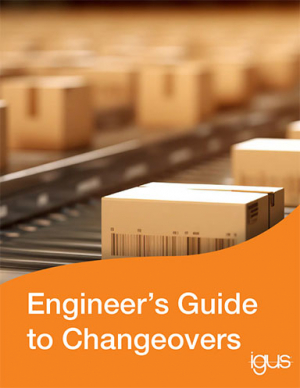
Subscribe to our FREE magazine,
FREE email newsletters or both!Latest News
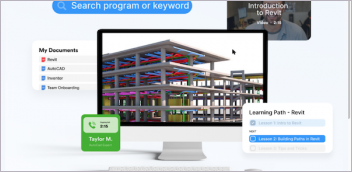
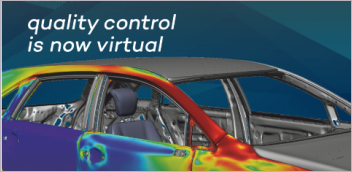
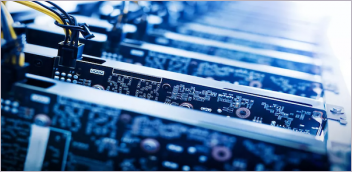
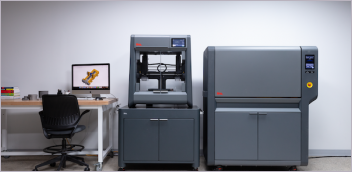