Engineering Toys—To Infinity and Beyond
As engineering design tools and methods advance, so does the toy industry in the design and production of toy products.

Game of Thrones game. Image courtesy of Western University.
Latest News
November 10, 2023
Today’s toy designers have many new and versatile tools available to them to expedite the design and production of toy products. They include cloud-based CAD, simulation and additive manufacturing (AM).
Chris Whipple is a senior project engineer for animatronics at Hasbro Inc. As a traditional CAD user, Whipple says that tools like Onshape are a huge leap forward over existing software workflows.
“Being cloud native offers a lot of benefits over traditional CAD. I love the fact that in the earliest stages of a project, I can just invite my partners in quality, costing, packaging, our model makers and other disciplines that might not directly influence the CAD to view my progress in real time,” says Whipple. “This provides us with the ability to collaborate in real time, as the design takes shape.
“Costing can point out assembly efficiencies, quality can spot possible trouble spots and packaging can keep an eye on package size all while the design engineer is actively developing the CAD, since the partners always have access to the latest and greatest version of the model,” he says. “Traditionally, this would require a meeting once the CAD is complete where each stakeholder would provide input after seeing the CAD for the first time, usually leading to rework.”
As engineering software tools become more affordable and more accessible to non-experts, the benefits will reach industries and applications that have previously not benefited, says Justin Hendrickson, director of product management at Ansys.
“Every time experimentation becomes faster, cheaper and easier, innovation goes up,” says Hendrickson. “The toy space is one of the most innovative and fast-moving industries, perhaps due to the sometimes short attention span of its customers. Michael McGinnis designed the Perplexus puzzle that can be found in almost every toy store in the world using Ansys tools. In his words, ‘I could not have conceived of the forms and the interconnectivity and in fact, just problem-solved, in the usual way, without SpaceClaim. Before that, I made things by hand.’”
Naveen Saini is the vice president and head of industry, consumer products, retail, services and public sector at Capgemini Engineering. Saini emphasizes that today’s toy designers and consultants are leveraging engineering software tools to enhance and expedite toy design, fostering safer, enduring and more sustainable toys that cater to fun and learning.
“Some toy companies employ 3D printing technology alongside engineering software to offer personalized toys,” says Saini. “This not only enhances the play experience but also reduces waste by producing only what is needed.”
More specifically, Saini adds that material science plays a crucial role in the development and manufacturing of toys.
“Toy designers and manufacturers must carefully select materials to ensure that toys are safe, durable and suitable for their intended purpose,” says Saini. “CAD tools linked with artificial intelligence (AI)] tools learning from R&D data can greatly benefit in accelerating product development in this space. Engineers are aiding toy designers in creating virtual prototypes, allowing them to quickly visualize and iterate their concepts. This accelerates the design process, reducing time to market.”
Saini says engineering tools enable designers to optimize the structural integrity and durability of toys. This ensures that toys withstand the rigors of play, reducing the likelihood of breakage and enhancing their longevity. By employing engineering analysis and simulations, designers can identify potential safety hazards and address them early in the design phase (that is, safety assurance), leading to safer toys for children.
Jason Lichtman is a senior technical specialist for design and manufacturing at Autodesk. He says toys today are more complex now than ever and that many toys also incorporate complex electronics.
“Designing and manufacturing smart toys is a difficult task, requiring cross-functional expertise in industrial design, mechanical engineering and electronics,” says Lichtman. “These interdisciplinary teams must collaborate to develop their products, despite competing needs and constraints. This back-and-forth can be especially challenging because each of these roles traditionally use different tools to complete their work.
“Additionally, many companies struggle with time to market,” Lichtman adds. “A typical consumer product takes 18 to 24 months to design, develop and start production. In today’s market, needs change rapidly and companies want the ability to respond quickly. While this has affected the entire consumer product sector, it is even more pronounced in the toy industry.”
The outcome is that toy companies must constantly find chances to develop their products faster.
“Thankfully, advances in design software technology enable multidisciplinary teams at toy companies to work and collaborate on a common cloud-connected platform, such as Autodesk Fusion 360,” Lichtman says. “Cloud platforms enable everyone on the team to work on the project concurrently, creating significant efficiencies throughout the product development process.”
In Pursuit of Better Toys With 3D Printing
With the advancement of engineering design tools and production methods such as (AM), toy products stand to benefit by producing safer toys, more enduring toys and often more sustainable toys. Plus, better design and production tools also help educational leaders in learning and development.
Joshua Pearce is the Thompson Professor of Innovation within the Ivey Business School and the university’s department of electrical and computer engineering at Western University. He helped research a study (mdpi.com/2227-7080/5/3/45) that says the toy and game market is projected to be US $135 billion. He points out that the study uncovered a robust outlook with use of 3D printing and filaments that such printing will use to reap benefits.
“To determine if 3D printing could affect these markets if consumers offset purchases by 3D printing free designs, this study investigates the 100 most popular downloaded designs at MyMiniFactory in a month,” he says. “Savings are quantified for using a Lulzbot Mini 3D printer and three filament types: commercial filament, pellet-extruded filament and post-consumer waste converted to filament with a recyclebot.”
Pearce notes that case studies cited in his research explored six common complex toys, as well as Lego blocks and the customization of open-source board games.
“All filaments analyzed saved the user over 75% of the cost of commercially available true alternative toys and over 90% for recyclebot filament,” Pearce says. “Overall, these results indicate a single 3D printing repository among dozens is saving consumers well over $60 million a year in offset purchases. The most common savings fell by 40% to 90% in total savings, which came with the ability to make novel toys and games.”
An Enduring Toy Story?
Overall, we can expect the toy industry to benefit in many ways. Consumers who purchase such toys stand to benefit from safer, better and more enduring toys. As new technology tools continue to evolve, many facets of toy design and manufacturing will benefit, now and into the future.
“Allowing our less design intensive but important partners like the costing and quality engineers real-time access to a model inevitably lead to more efficient, robust and safe designs,” says Hasbro’s Whipple. “The ability to monitor progress in real time, identify room for improvement and influence the design as it develops will save time through unnecessary meetings and rework, save costs in terms of development hours and product cost, and generally lead to more robust, more well-rounded and overall better products. This is particularly important for toys as our end users, generally children, are very unapologetic in how they use and handle our products, so robust design is critical.”
Autodesk’s Lichtman says that now, thanks to advanced engineering tools such as AutoCAD, many new and innovative technologies exist—3D printing, generative AI, new and better materials. Such tools and methods help sculpt an optimistic future for toy design and manufacturing.
“For many decades, advanced product development tools were prohibitively expensive to adopt and exceedingly difficult to learn,” Lichtman says. “This meant the most advanced technology could only be accessed by a select few individuals on a team, often on dedicated workstations. If other team members needed access to those tools, they had to request the services of their more specialized counterparts and wait in a queue until that resource became available.
“However, democratization of advanced tools, such as [finite element analysis (FEA)], has put more power into the hands of the average designer and engineer,” Lichtman adds. “Instead of sending files to someone else and waiting for an answer, they now have access to these tools themselves, within their existing CAD environment, enabling them to get an almost immediate answer to their design challenge. Simply put, democratization puts advanced design technology in more hands, thereby multiplying the beneficial impact the technology has.”
More Ansys Coverage
More Autodesk Coverage
Subscribe to our FREE magazine,
FREE email newsletters or both!Latest News
About the Author

Jim Romeo is a freelance writer based in Chesapeake, VA. Send e-mail about this article to DE-Editors@digitaleng.news.
Follow DE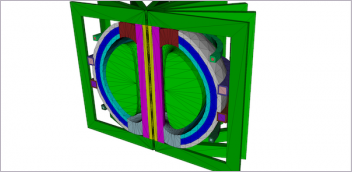
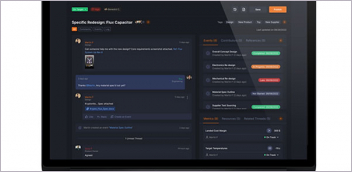
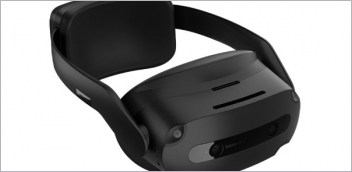
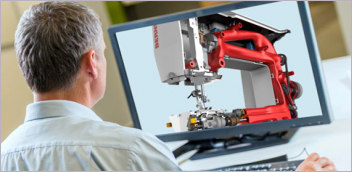